Infrared Roof Moisture Surveys
The most accurate and efficient method for moisture detection in commercial roofing systems. Infrared cameras can “see” the wet insulation in the majority of common roof types.
The industry standard for moisture analysis in most commercial roofing applications for the past several decades has been the Infrared Roof Moisture Survey. Using the heat absorbed into the roof system during a warm, sunny day, the infrared cameras are able to detect differences in the temperatures of wet and dry insulation as the roofs cool off in the evening.
Following sundown, the infrared cameras can “see” the wet insulation as it retains the day’s heat because it is a better thermal conductor than the dry insulation. The wet areas are outlined on the roof surface with marking paint, sized up, and transposed to a field drawing. Moisture readings from our nuclear moisture gauges are then used to verify the moisture content in each wet area. If the roof is not under warranty, a core sample will be taken as a final verification of the accuracy of the survey and properly patched.
Infrared surveys can only detect moisture in the upper roof of a multi-layered system but can be used in conjunction with a Nuclear Roof Moisture Survey to determine the moisture content of both layers.
Infrared Moisture Surveys include…
- Rooftop moisture analysis
- Infrared moisture survey of all applicable roof areas
- Verification of all wet areas using nuclear moisture gauge
- 1-2 core samples taken in wet area(s) as final verification
- Rooftop marking of wet areas, nuke readings, and core sample(s)
- Written report including
- Moisture survey operating principles and procedures
- Roof construction and moisture content of core samples
- Quantification of all moisture laden insulation
- Thermograms (thermal images) of select wet areas
- Color CAD drawing including
- Roof plan to scale of all roof areas by numerical designation
- Locations of all moisture laden areas, nuke reading, and core samples
- PDFs and two hard copies of report and drawing
What Roofs Can Be Scanned With This Method?
Can Be Scanned
- All Single-Ply Membranes
- Smooth & Gravel Surface Asphalt BUR
- 1-2 Ply Modified Bitumen Membranes
- Liquid Membranes
Must Be Scanned
- Silicone/Foam Roofs
Can't Be Scanned
- Ballasted EPDM Roofs
- 3-4 Ply Modified Bitumen Membranes
- Metal Roofs
- Aluminized Coated Roofs
- “Green” Roofs
- Roofs With Multiple/Thick Membranes
- Roofs Without Insulation
- Roofs During Cold Weather
Benefits of a Moisture Survey
- Locate moisture laden insulation
- Isolate leak source areas and identify potential defects
- Determine if a roof is in need of targeted repair or full replacement
- Accurately determine the scope of work prior to issuing bid documents
- Eliminate unknowns to dramatically cut down on up-front costs
- Eliminate costly extras and change-orders during roof projects
- Identify existing dry insulation to be incorporated into a replacement system, reducing overall costs and material waste.
- Check the integrity and workmanship of a new roof system or repair
- Ensure a manufacturer’s warranty will be issued upon completion of a new roof system
More about IR Surveys…
Infrared Roof Moisture Surveys have specific daytime environmental requirements to produce distinguished thermal patterns that can be easily viewed through the cameras, so the first step of a successful survey is selecting the appropriate date to perform the scan. Ideal daytime weather conditions include a desireable combination of high temperatures, strong sunshine, low wind speed, and an absence of rain or snow. The cameras are unable to read through concentrations of water on the roof surface, so roofs should be given adequate time to drain/evaporate from a previous rain event prior to the survey. Because the surveys require the roofs absorb a certain degree of heat to produce accurate results, IR surveys are typically not possible in the wintertime and should be scheduled between March and November to avoid any weather-related delays.
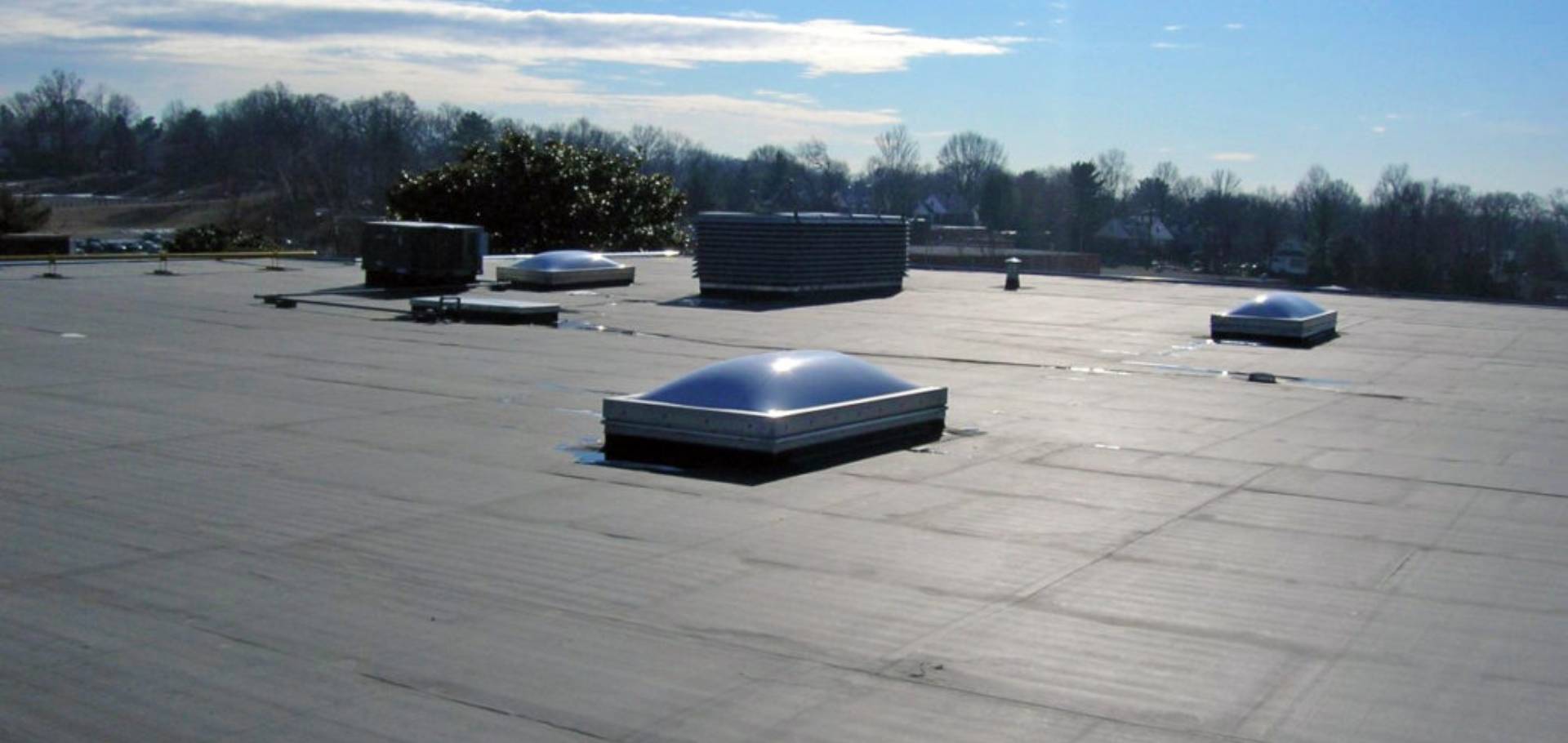
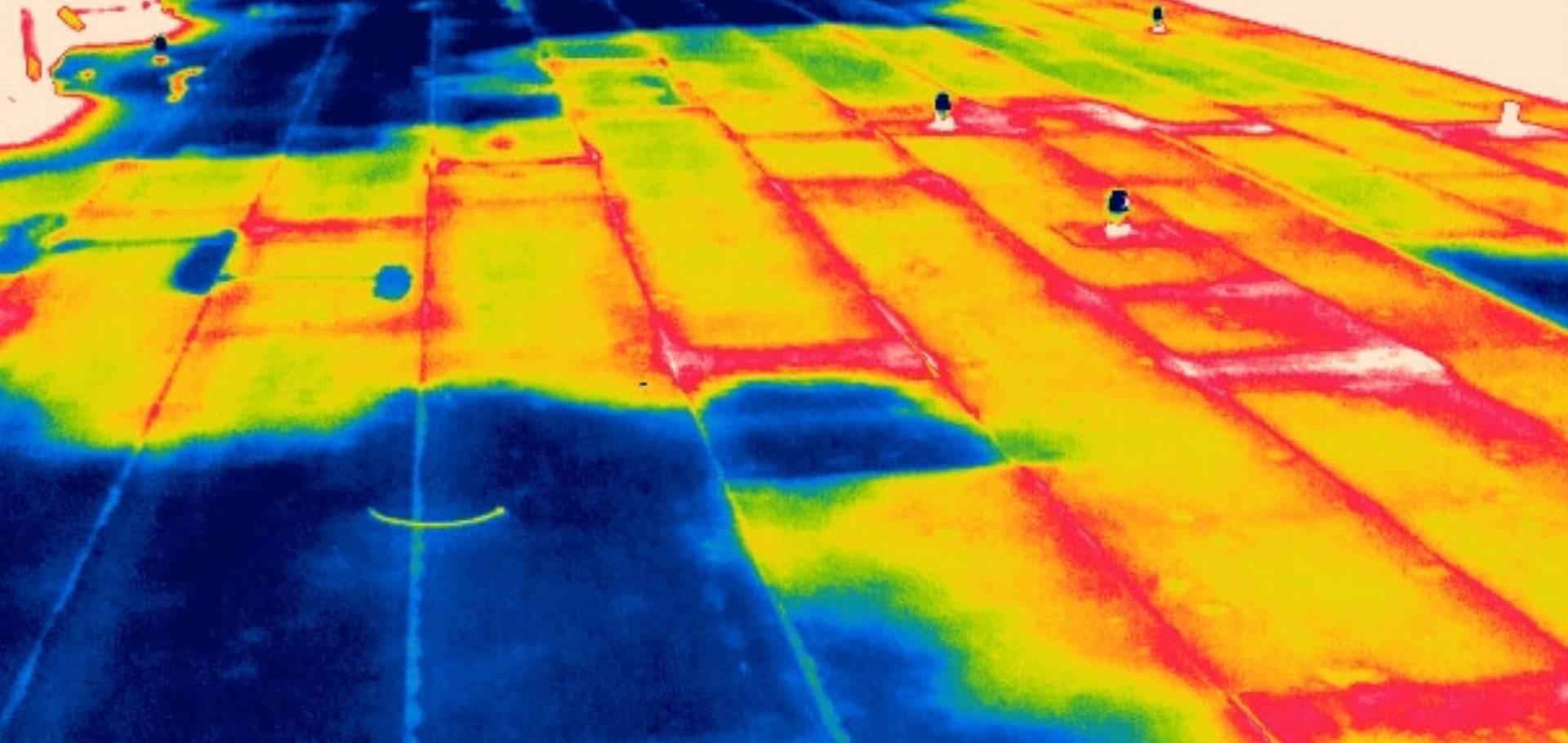
Once an appropriate day has been selected, the survey begins immediately following sundown. The lack of UV radiation from the sun combined with decreasing temperatures causes the dry insulation to shed the majority of the heat absorbed during the day while the wet insulation retains it for several more hours. This retained heat affects the surface temperature of the membrane and is visible in the camera’s display as spots of bright orange/yellow compared to the surrounding dry areas of dark blue/purple. These areas are then outlined on the roof surface in marking paint and the dimensions of the areas are determined. The wet areas are then transposed to a field drawing in relation to their approximate size, shape, and location on the roof.
Once locations of subsurface moisture are identified with the cameras, the wet areas are verified using our nuclear moisture gauges. The gauges return a numerical value relative to the amount of moisture present below the devices. Nuclear readings are taken inside and immediately outside of each wet area to show the elevated readings within the moisture contours compared to the lower readings of the surrounding dry roof area. As a final verification of accuracy, one or two core samples are taken in a wet area to confirm that the insulation is indeed moisture laden and then patched in accordance with the membrane type.
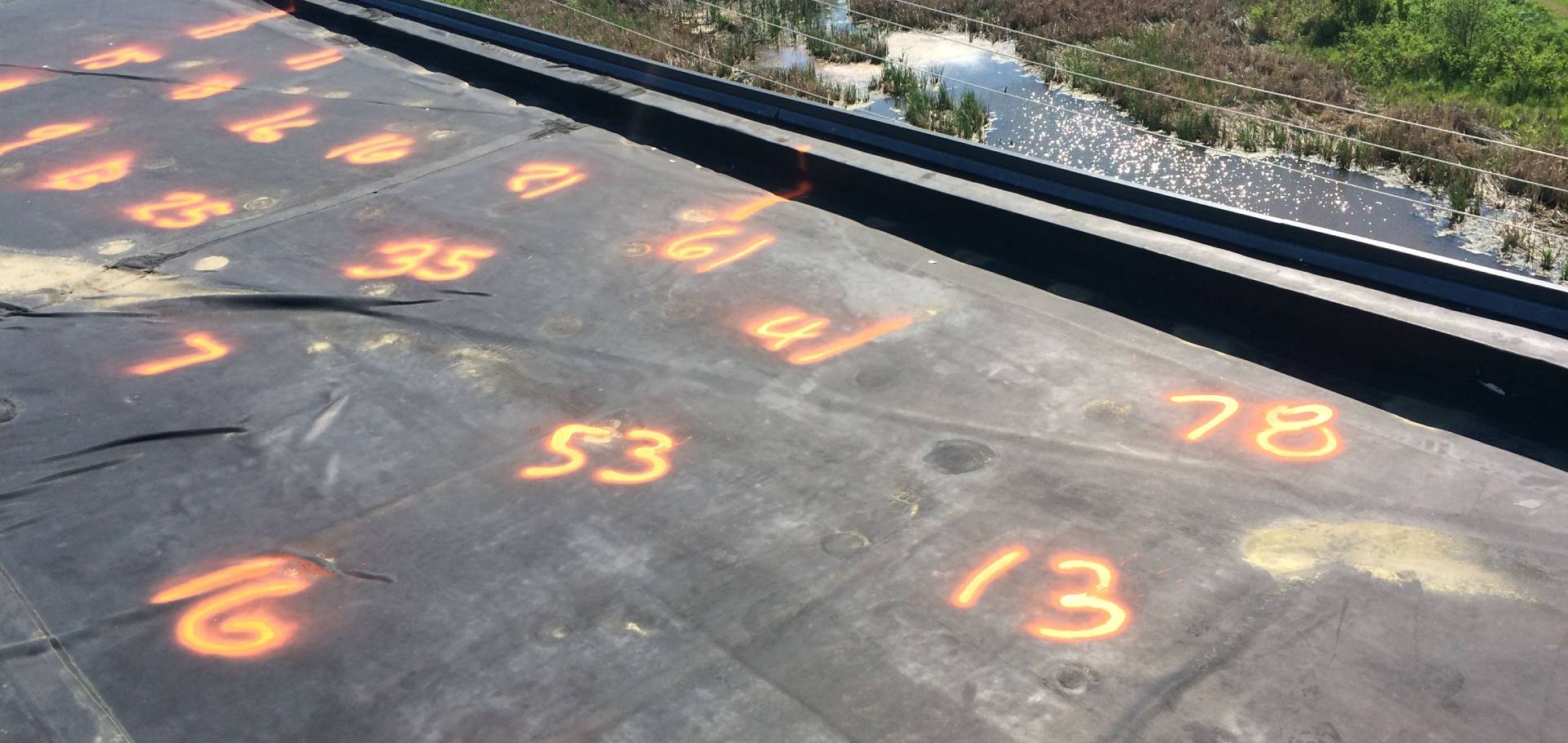
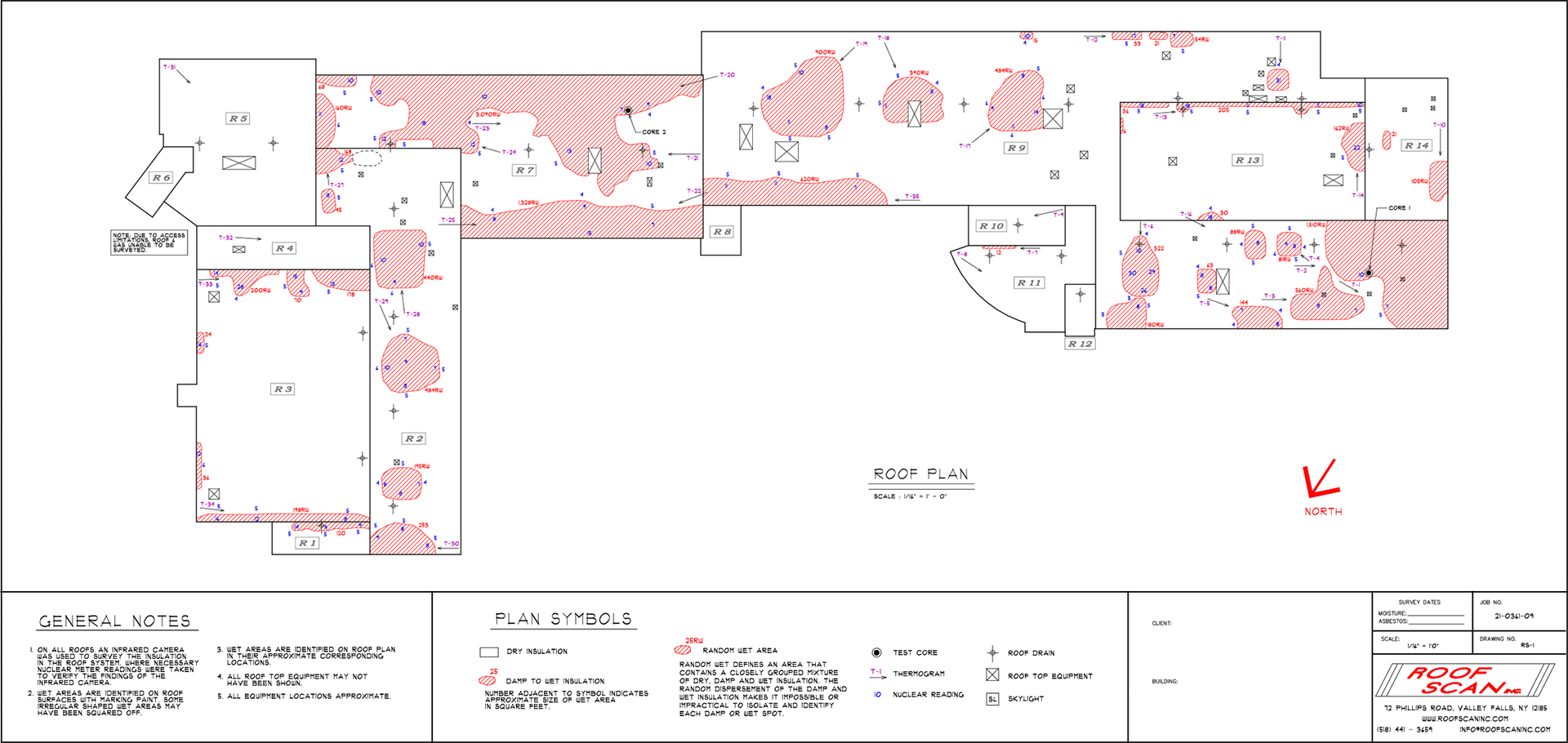
Back in the office, the field drawing is reproduced in a multi-colored CAD drawing showing the locations of all wet areas, nuke readings, and core samples. The dimensions of the individual wet areas are added up and a report is generated containing all of the details of the survey and the square footages of moisture laden insulation for each roof area and the project total.
Related Services
Nuclear Roof Moisture Survey
An accurate alternative test method for locating moisture laden insulation in more challenging situations.
Asbestos Sampling and Testing
Roof top sampling of suspect building materials by licensed inspectors and testing by a certified laboratory facility.
Construction Documentation
Detailed documentation of materials, thicknesses, attachment methods, and structural deck systems.